Digital technology's reshaping textile design, allowing you to create stunning fabrics with ease. Techniques like digital textile printing and 3D modeling let you visualize and customize designs while minimizing waste. Methods like DTG and DTF printing enhance color accuracy and detail, making every piece unique. You'll also find that sustainability plays a big role in this evolution. Discover how these innovations can elevate your designs and transform your creative process further.
Key Takeaways
- Advances in digital textile printing technologies like DTG and DTF enable the creation of intricate and vibrant designs with high accuracy.
- 3D modeling enhances the design process by allowing visualization and rapid iteration, reducing waste and improving collaboration with manufacturers.
- AI and machine learning automate design generation, offering personalized and customizable textile solutions that cater to individual consumer preferences.
- Sustainable practices in digital textile design, such as on-demand production, minimize waste and reduce water usage compared to traditional methods.
- Tools like Adobe Substance 3D integrate digital and physical fabrics, ensuring photorealistic results and seamless design-to-production workflows.
The Evolution of Digital Textile Design

As technology advances, the evolution of digital textile design has transformed the way we create and produce fabric patterns.
You'll notice that technology innovations like AI and machine learning automate your design processes, enabling you to generate intricate designs instantly.
Digital textile printing is booming, projected to grow considerably due to the rising demand for sustainable fashion and customizable solutions.
In industries like apparel and footwear, you can replace physical samples with digital fabrics, enhancing consumer experiences with simulated designs.
Innovations in printing techniques, such as direct-to-garment (DTG) and direct-to-fabric (DTF), resolve challenges in achieving high-definition designs and accurate colors.
Using PDF files in your design workflow also guarantees seamless collaboration and precise color management for personalized creations.
Exploring Digital Fabric Printing Techniques
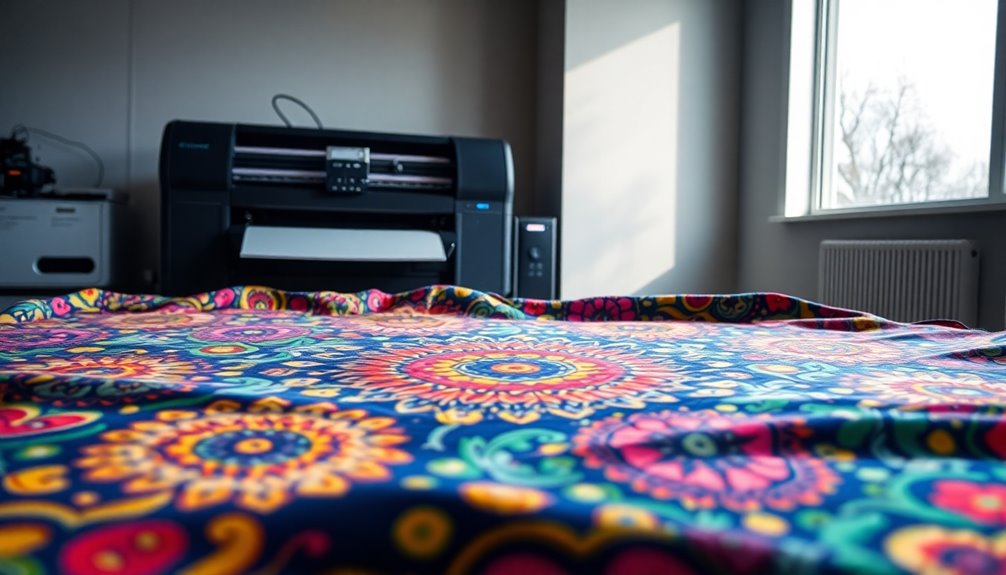
Digital fabric printing has revolutionized the textile industry, offering innovative techniques that cater to diverse design needs.
You'll find three primary production methods: direct-to-garment (DTG) printing for intricate designs, roll-to-roll (DTF) printing for large-scale production, and cut-and-sew printing.
DTG allows you to create high-resolution, vibrant designs directly on garments, perfect for custom apparel. Achieving consistent color reproduction is essential, and integrating PDF technology helps manage complex design variations, ensuring seamless collaboration between you and other designers.
These digital textile printing techniques support on-demand production, greatly reducing fabric waste and enabling personalized designs that reflect individual customer preferences.
Embracing these sustainable practices not only benefits the environment but also elevates your creative potential in textile design.
The Role of 3D Modeling in Textile Creation
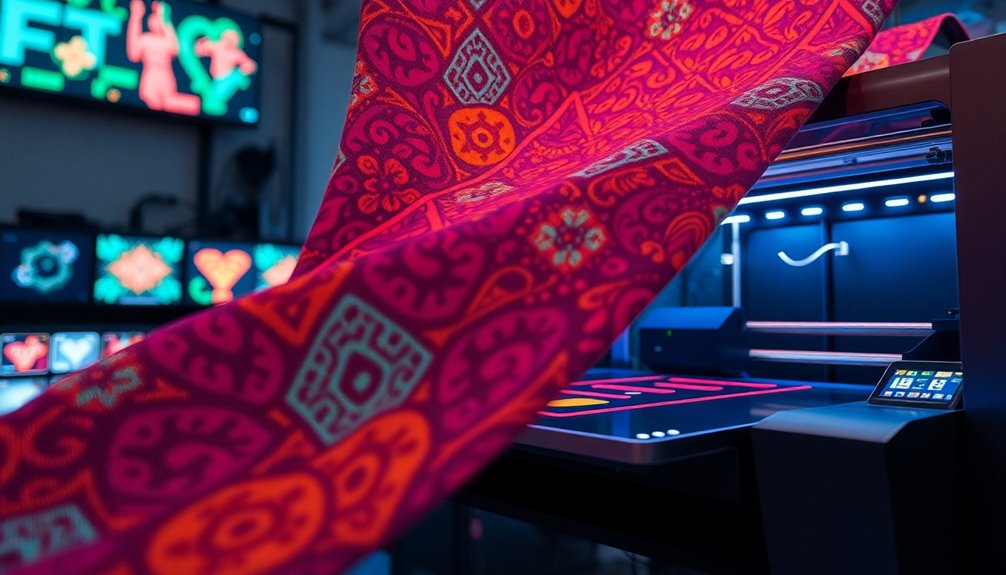
3D modeling transforms how you approach textile design by offering precision and flexibility.
You can create intricate patterns and visualize them before committing to physical samples, which enhances accuracy and reduces waste.
Plus, it streamlines collaboration with manufacturers, speeding up the entire process from concept to creation.
Benefits of 3D Modeling
The integration of 3D modeling in textile design revolutionizes the way designers approach their creative process. You can visualize and manipulate fabric patterns and textures digitally, which streamlines the design process and cuts down on physical prototypes.
This technology allows for rapid iteration and customization, catering to consumer demand for unique products. By simulating how fabrics behave in real-world conditions, you can predict draping, stretch, and fit before production.
Combined with digital textile printing, 3D modeling helps create intricate, high-quality patterns directly on fabrics, enhancing production efficiency.
Furthermore, adopting 3D modeling supports sustainability by reducing the number of physical samples, ultimately lowering the carbon footprint associated with traditional garment manufacturing.
Enhancing Design Accuracy
While traditional textile design often involves guesswork and multiple iterations, embracing 3D modeling transforms this process into a precise and efficient endeavor.
With 3D modeling, you can create intricate textile patterns digitally, greatly enhancing design accuracy and reducing waste in textile production. Advanced software allows you to simulate how fabrics will drape and behave, ensuring a better fit before manufacturing starts.
Integrating 3D body scans means you can tailor designs to individual body shapes, boosting customer satisfaction and minimizing returns.
By utilizing digital inkjet technologies alongside 3D modeling, you can quickly prototype unique textiles, accelerating the design-to-manufacturing workflow while maintaining high accuracy.
This innovative approach not only optimizes production but also paves the way for smart textiles in your designs.
Bridging the Gap Between Virtual and Physical Fabrics

As designers increasingly embrace digital tools, bridging the gap between virtual and physical fabrics becomes essential in the textile industry.
Collaborations like that between Cotton Incorporated and Adobe are pivotal, as they use Adobe Substance 3D applications to unify digital and physical materials. This technology enables the creation of digital fabrics that accurately reflect manufacturable textiles, ensuring photorealistic results.
By employing scan and procedural techniques, you can integrate these materials into various fashion design tools and 3D applications seamlessly. The streamlined digitization workflow allows for rapid design creation, often within just two days. Additionally, the use of advanced infusion machines can inspire unique fabric textures that mimic organic materials found in nature.
Sustainability Through Digital Innovations
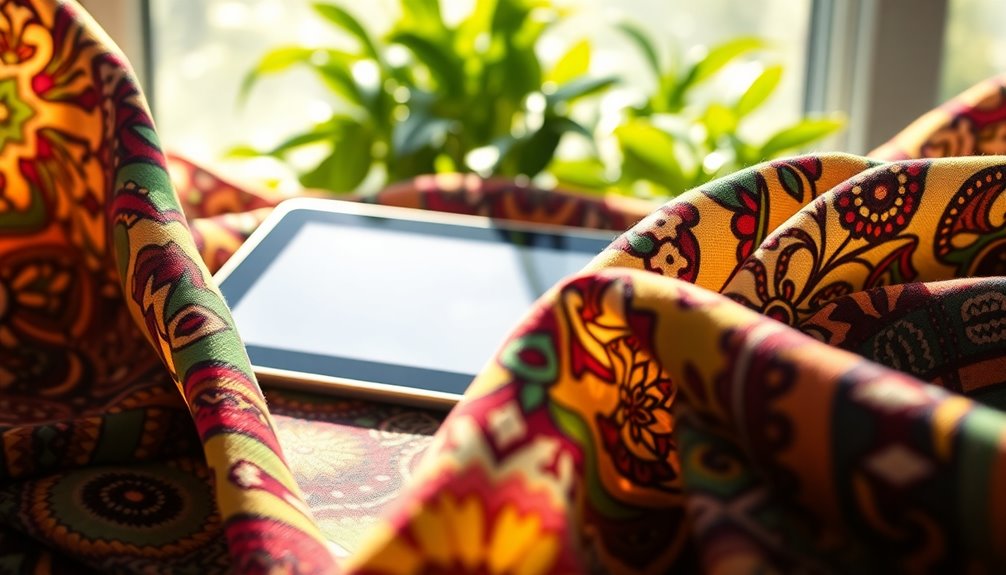
As you explore digital textile designs, consider how eco-friendly printing solutions can reshape the industry. These innovations not only reduce waste but also enhance the sustainability of your creations. Additionally, advancements in solar energy technologies can provide clean power to manufacturing processes, further promoting environmental responsibility.
Eco-Friendly Printing Solutions
Digital textile printing (DTP) is revolutionizing the fashion industry by offering eco-friendly solutions that align with modern sustainability demands.
By utilizing eco-friendly inks and innovative technologies, DTP reduces water usage and supports environmentally responsible practices.
You can expect:
- Customizable printing solutions that cater to your unique preferences without excessive waste.
- Sustainability in production, as brands respond to consumer demand for ethically produced textiles.
- Waste reduction through on-demand production, eliminating the need for large inventory runs.
With DTP, companies can adapt quickly to market trends while minimizing their environmental footprint. Additionally, adopting integrated pest management practices in textile production can further enhance sustainability by reducing chemical usage.
Embracing these eco-friendly printing solutions not only benefits you but also contributes to a healthier planet.
Join the movement towards a more sustainable fashion future!
Waste Reduction Techniques
While traditional textile production often results in significant waste, innovative waste reduction techniques through digital textile printing (DTP) are changing the game.
With DTP, you can enjoy on-demand production, which cuts down fabric waste by eliminating the need for large production runs.
By utilizing automation and AI, you streamline design and manufacturing workflows, enhancing efficiency and reducing material waste.
The integration of variable printing capabilities allows for personalized designs, minimizing excess inventory.
Plus, the use of eco-friendly inks not only lowers water usage but also decreases the carbon footprint of the printing process. Additionally, the emphasis on sustainable forestry in wood stove usage aligns with the growing demand for eco-conscious practices in various industries.
The Future of Fashion Design: Merging Digital and Traditional Methods
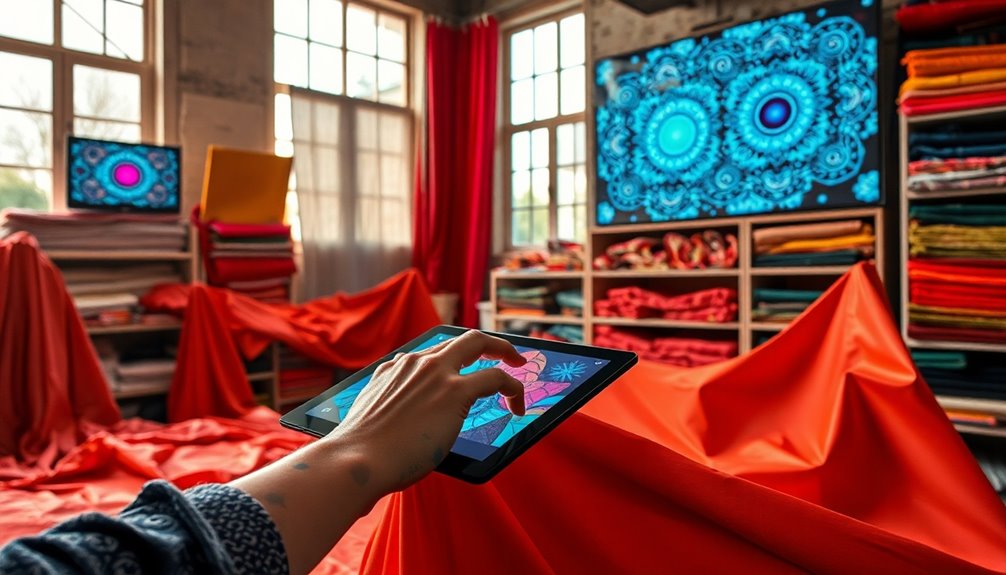
Fashion design is evolving rapidly, blending traditional methods with cutting-edge digital technologies. This seamless integration allows you to create stunning designs that resonate with modern consumers.
Here's what you can expect in the future:
- Enhanced design accuracy through digital textile printing, ensuring your virtual samples reflect physical materials perfectly.
- Increased customization options powered by AI and machine learning, letting you tailor designs to individual preferences.
- Eco-friendly practices as on-demand production reduces waste, supporting sustainable fashion initiatives.
As you explore this exciting fusion of digital and physical spaces, you'll find that tools like Adobe Substance 3D are revolutionizing the way you approach textile design, making it more efficient and innovative than ever before.
Skills for the Next Generation of Textile Designers
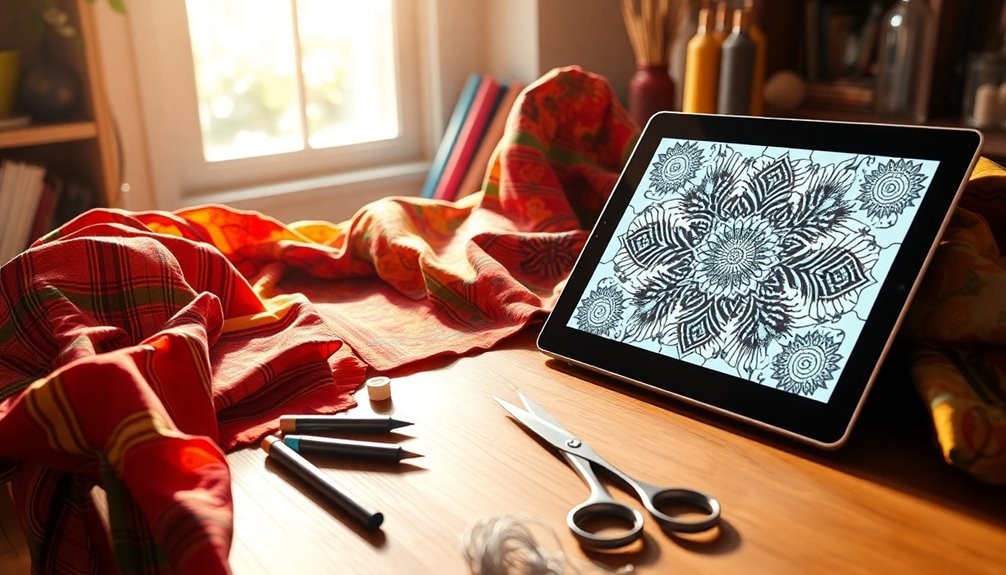
As the landscape of textile design shifts, mastering a blend of traditional skills and modern technologies becomes essential for the next generation of designers. Familiarity with digital fabric design software like Adobe Substance 3D helps streamline your design process. Understanding digital textile printing techniques, such as DTG and DTF, allows you to produce high-quality, customized designs with less waste. Don't overlook the importance of smart textiles and wearable technology, which let you integrate electronic components into fabrics, enhancing functionality. Finally, proficiency in data-driven personalization and customization will meet the growing demand for unique products.
Skill | Importance | Tools/Technologies |
---|---|---|
Digital Fabric Design | Streamlines design process | Adobe Substance 3D |
Textile Printing | Customization & waste reduction | DTG, DTF |
Smart Textiles | Enhances functionality | Wearable technology |
3D Printing | Innovation & unique structures | 3D printing technology |
Data Utilization | Personalization | AI, machine learning |
Frequently Asked Questions
What Is Digital Design in Textiles?
Digital design in textiles lets you use software and technology to create intricate patterns and designs for fabrics.
You can apply detailed designs directly onto garments using techniques like Direct-to-Garment printing, which streamlines production and reduces waste.
This approach also enables you to produce personalized designs on-demand, supporting sustainability.
How Is Technology Used in Textiles?
Imagine weaving a tapestry of innovation where threads of technology dance with creativity.
In textiles, you harness smart fabrics that adjust to your body's needs, while digital printing lets you splash vivid designs onto fabric like an artist on canvas.
Innovations like 3D printing and AI transform how you prototype and personalize, minimizing waste.
With advanced materials, you create responsive textiles that not only look stunning but also interact with the world around you.
What Is a Technique in Producing a Fabric or Textile Design of the Cloth?
One effective technique for producing fabric designs is direct-to-garment (DTG) printing.
With this method, you apply intricate designs directly onto the cloth, achieving vibrant colors and fine details. It's perfect for creating custom garments, as you can easily experiment with various patterns and styles.
Plus, it allows for short production runs, so you can bring your unique vision to life without committing to large quantities. You'll love the creative freedom it offers!
Which Software Is Used for Textile Designing?
Imagine crafting a masterpiece, where your imagination can truly come alive.
When it comes to textile designing, you’ve got a range of powerful software at your fingertips. Adobe Photoshop and Illustrator let you manipulate patterns and colors with ease. Additionally, programs like CorelDRAW and Procreate offer unique features that cater specifically to textile artists, allowing for intricate designs and vibrant illustrations. To truly master your craft, it’s essential to understand color theory for textile design, as it enables you to create harmonious combinations that enhance your work. With these tools and knowledge, you can bring your textile visions to life, pushing the boundaries of creativity and innovation.
For pattern making, CAD software like Gerber AccuMark is essential. If you want to visualize garments, try 3D design software like Clo3D.
Each tool enhances your creativity, bringing your fabric visions to life!
Conclusion
As you explore the world of digital textile design, you might just find yourself caught between the pixels and the patterns, where creativity knows no bounds. Imagine stumbling upon a stunning fabric that perfectly matches your vision, thanks to 3D modeling and innovative printing techniques. It's exciting to think that as technology advances, you can merge traditional craftsmanship with digital flair, paving the way for a sustainable future in fashion that's uniquely your own. Immerse yourself and create!